The work focuses on the importance of bead geometry modelling in Directed Energy Deposition Additive Manufacturing. Bead dimensions and shape are deciding factors for the mechanical properties, accuracy, and surface roughness of the 3D printer part. CFD simulation in FLOW-3D AM enables accurate prediction of the powder deposition, melting and solidification and lets the engineers and scientists look into the influence of process parameters on the final shape of the deposited track. An optimization tool FLOW-3D (x) is further used to automatically choose the process parameters that yield compact bead shape at maximum building rate. For more information on how FLOW-3D AM can simulate DED processes visit [ Ссылка ].
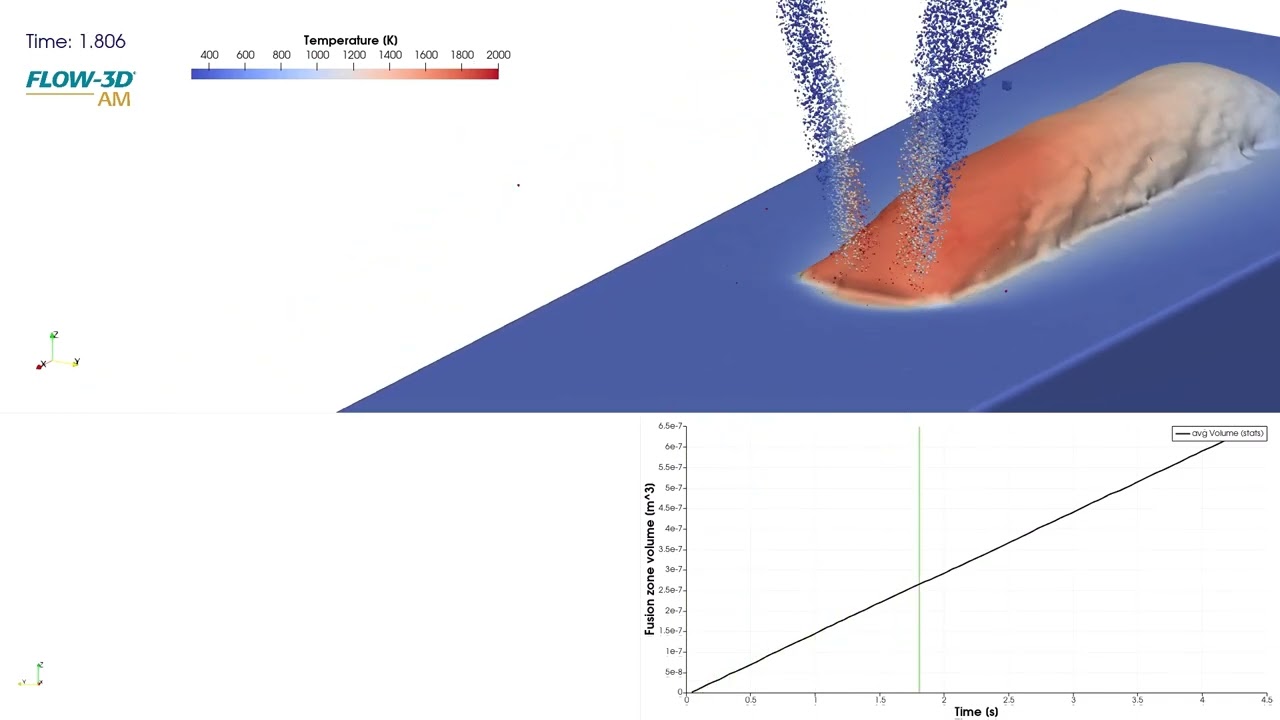