Collaborative robots in manufacturing can take the mundane and stressful in stride. Excelling at dull, dirty, and dangerous tasks is what they do best.
Consider cobots scaled down versions of other familiar robots already utilized in manufacturing facilities around the world.
Bench-top models resemble miniature articulated robots, at 3 to 4 feet in length. They are agile, lightweight, and customizable to an array of tasks. These same robots can also be mounted to mobile platforms. This can expand the cobot’s range of operation, assuming many different assembly tasks with quick changeover from station to station.
Mobile cobot examples are also gaining momentum ferrying materials and components to staging areas, so that staff don’t waste time walking from their bench to picking locations in your facility. Manufacturing and distribution centers gain incredible productivity when these useful robots can carry weights no human possibly could between storage and staging areas. The result is more employee engagement regarding the tasks at hand, fewer opportunities for accidents, and less time wasted walking the floor.
Mobile robots also make managing inventory much easier on your operations. They can complete non-stop audits of inventory, suggest amended sorting based on flow of goods, and other efficiency opportunities based on the data flowing from their sensors into your ERP system. Businesses can then bring planning and scheduling to greater levels of efficiency, driving supply chain management like never before.
Chat bots answer visitor inquiries on your website and report back to your CRM with visitor profile data.
Robotic process automation (RPA) routines fall into this category, too. They handle repetitive data-entry and admin tasks at an exponentially faster rate than humans. Not only does this example enable immense cost savings for large operations, but smaller businesses can remain competitive by handling more tasks with fewer costs sunk into non-revenue generating activities.
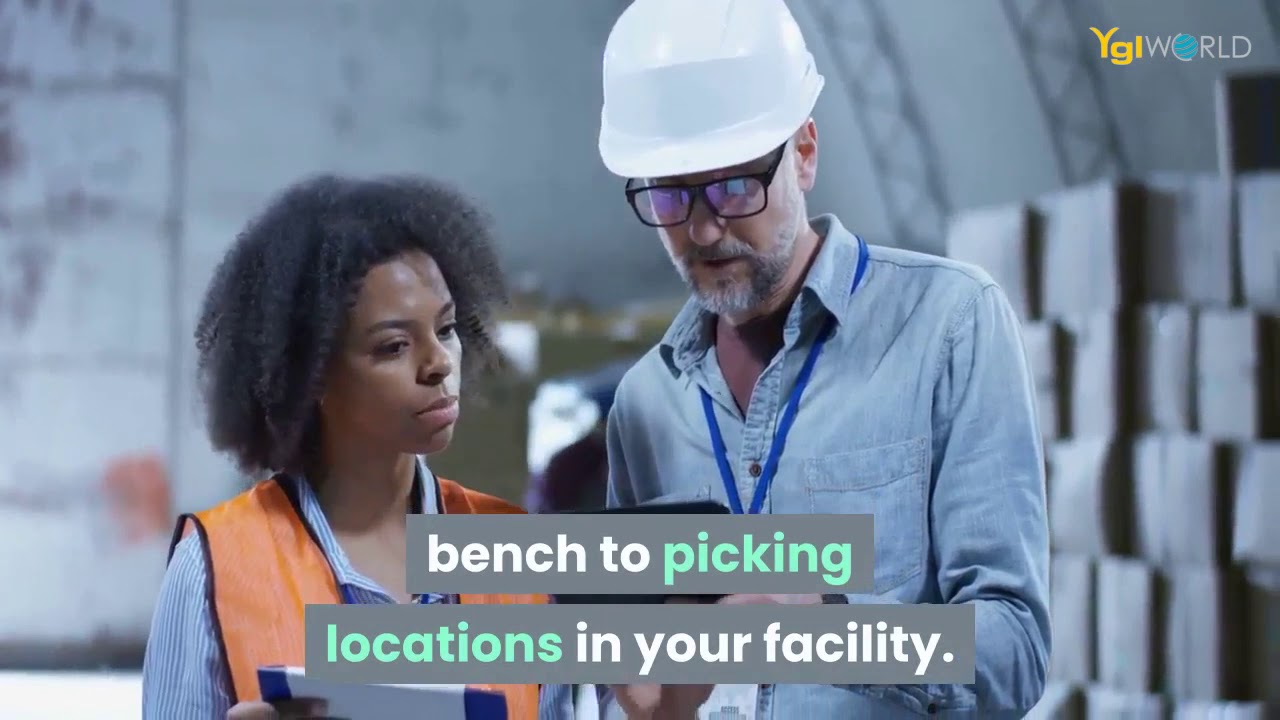