Dear Partners, our company «KONSORT» is ready to offer you the solution of post terminals full automation. At the moment we have a solution that will allow you to sort «large» dispatch (2-80 kg) with a capacity of 7000 parcels per hour, «small» (0,1-2 kg) 9000 parcels.
1. Shipments are laid out by operators on telescopic conveyors, there is the possibility of simultaneous
unloading from six vehicles at once. Further, the consignments along the lifting conveyors call into the
main sorting line, which is at a height of 3.3mt.
2. With the help of the algorithm for the operation of conveyors, shipments are built into the «correct»
queue for further scanning.
3. The process of scanning parcels occurs in five planes, which practically excludes the possibility of
errors in the scanning device (Sick, Germany) when reading the barcode. After the parcels have passed
through the scanner, the main line already «understands» in which direction the parcel needs to be
redirected from the given directions.
4. Redirection occurs in automatic mode using conveyors «swivel sorter» which have the ability to
redirect parcels at an angle of 45 degrees in both of directions. With help of this mechanism, using
small areas, we were able to double the number of options for directions. This line has the ability to sort
28 directions.
5. The line provides for possible «not scanned» cargo due to damaged, doubled barcodes, not removing
parcels from a full port. Such shipments go to the end of the line and end up on the line Overflow by
which they fall for re-sorting
6. Cargoes, on which the barcode is completely damaged and cannot be scanned, falls into the zone of
manual barcode application. After that, it is re-sent to the line.
7. Polyboxes with a small load will also move through the main line. A separate direction has been allocated
for them, along which the boxes will fall into the sorting of small parcels area.1. Shipments are laid out by operators on telescopic conveyors, there is the possibility of simultaneous
unloading from six vehicles at once. Further, the consignments along the lifting conveyors call into the
main sorting line, which is at a height of 3.3mt.
2. With the help of the algorithm for the operation of conveyors, shipments are built into the «correct»
queue for further scanning.
3. The process of scanning parcels occurs in five planes, which practically excludes the possibility of
errors in the scanning device (Sick, Germany) when reading the barcode. After the parcels have passed
through the scanner, the main line already «understands» in which direction the parcel needs to be
redirected from the given directions.
4. Redirection occurs in automatic mode using conveyors «swivel sorter» which have the ability to
redirect parcels at an angle of 45 degrees in both of directions. With help of this mechanism, using
small areas, we were able to double the number of options for directions. This line has the ability to sort
28 directions.
5. The line provides for possible «not scanned» cargo due to damaged, doubled barcodes, not removing
parcels from a full port. Such shipments go to the end of the line and end up on the line Overflow by
which they fall for re-sorting
6. Cargoes, on which the barcode is completely damaged and cannot be scanned, falls into the zone of
manual barcode application. After that, it is re-sent to the line.
7. Polyboxes with a small load will also move through the main line. A separate direction has been allocated
for them, along which the boxes will fall into the sorting of small parcels area.
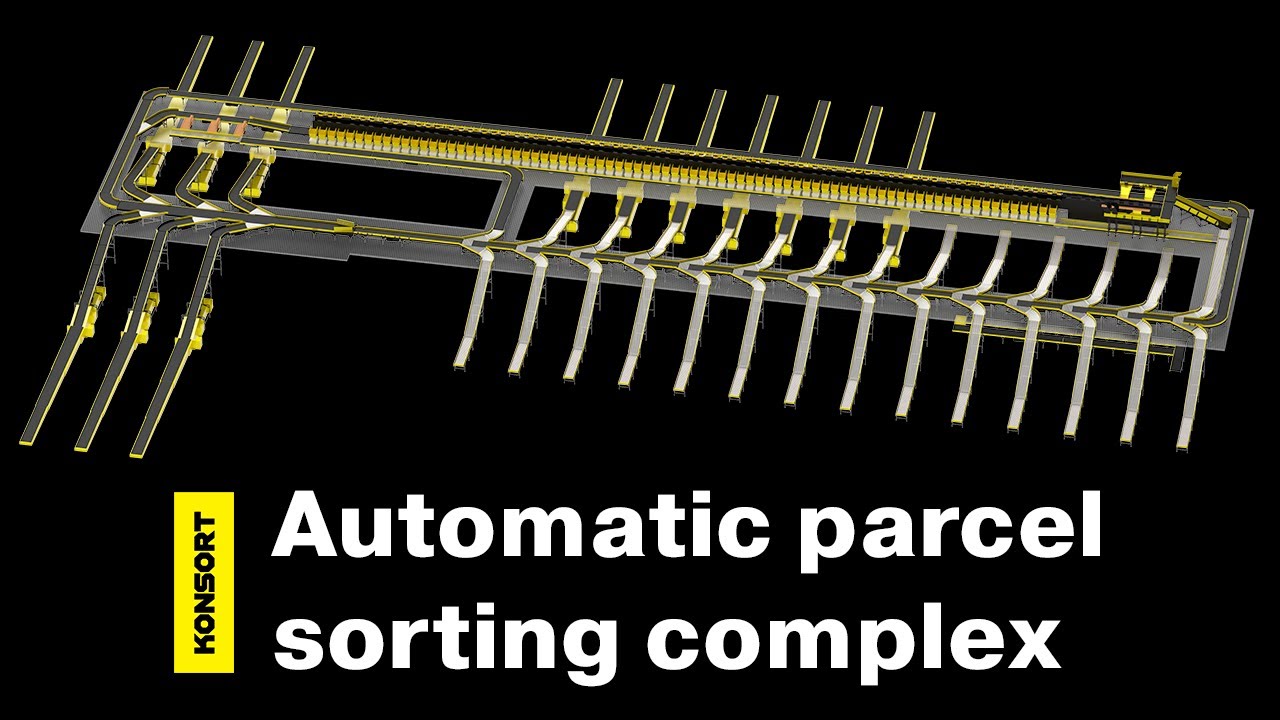