Stainless steel ball valves utilize a machined or soldered spherical ball to block or enable fluid flow. The ball is connected to a stem which in turn is connected to either a handle (for manual use) or a motor for automated use. Turning the stem rotates the ball and either exposes the bore to the fluid path or blocks it.
With their superior corrosion resistance and sturdy construction stainless steel ball valves are commonly used for high pressure saline or corrosive media applications. Industrial grade valves are usually rated to 1000 psi or higher.
Stainless steel ball valves are either a “trunnion pin” or “floating ball” design. In a trunnion pin design, the ball is held in place by a pin at the base of the valve body. This design is more common for larger valves (greater than 6” in diameter). In a floating pin design, as the name implies, the ball “floats” atop of and is held in place by the valve seats.
Some features that differentiate higher quality valves include being cast from a higher grade of stainless (316 vs 304), a stainless steel ball (316 vs other alloys), a solid vs plated steel ball, and high quality sealing materials. Sealing materials can vary by application but reinforced Teflon (RTFE) is commonly used as it provides excellent sealing performance for a wide range of applications and is chemically inert.
Explosion proof actuators are for use in potentially flammable environments. They are specially designed so they will not act as an ignition source and are certified as such. In practice this means not only will an explosion proof actuator suppress any spark or ignition source, but the enclosure must also be able to contain an internal explosion with no flame or spark escaping.
In the US the most common certification is the UL Class/Division standard, where Class refers to the type of explosion hazard (gaseous (Class I) or dust (Class II)) and Division refers to whether or not the hazard is normally present (Div I) or not normally present (Div II).
The EU generally uses the ATEX standard which classifies application by environment (type G for gases and type D for dusts) and zones which roughly correspond to the UL system. In addition, there is a third standard, IECEx, which is intended to be for global use. It is an industry standard (as opposed to a government one) and is quite similar to ATEX. However, unlike ATEX, EU countries are not required to adopt it.
Explosion proof design techniques include circular field joints to better withstand explosion pressures, long faying surfaces to suppress flame travel and internal compartmentalization to ensure explosion containment.
Positioning actuators throttle the valve to the desired position via an internal servo-controller. Changing the input signal (usually 4-20mA or 0- 10V) results in a corresponding and proportional change in the position of the valve. If there is a total loss of power the valve remains in the last known position. If the control signal is lost, the actuator can be programmed to fail open or fail close.
Electric positioning actuators come in a variety of torque ratings, from as low as 20Nm to 600Nm or more. Common voltages are 24VDC and 120VAC.
Some features that differentiate higher quality electric positioning actuators include a self-calibrating controller, an all-metal gear drive, a weatherproof enclosure (normally IP 67 NEMA 4X or higher), a thermostatic heater to prevent internal condensation, a manual override mechanism and a dome position indicator.
[ Ссылка ]
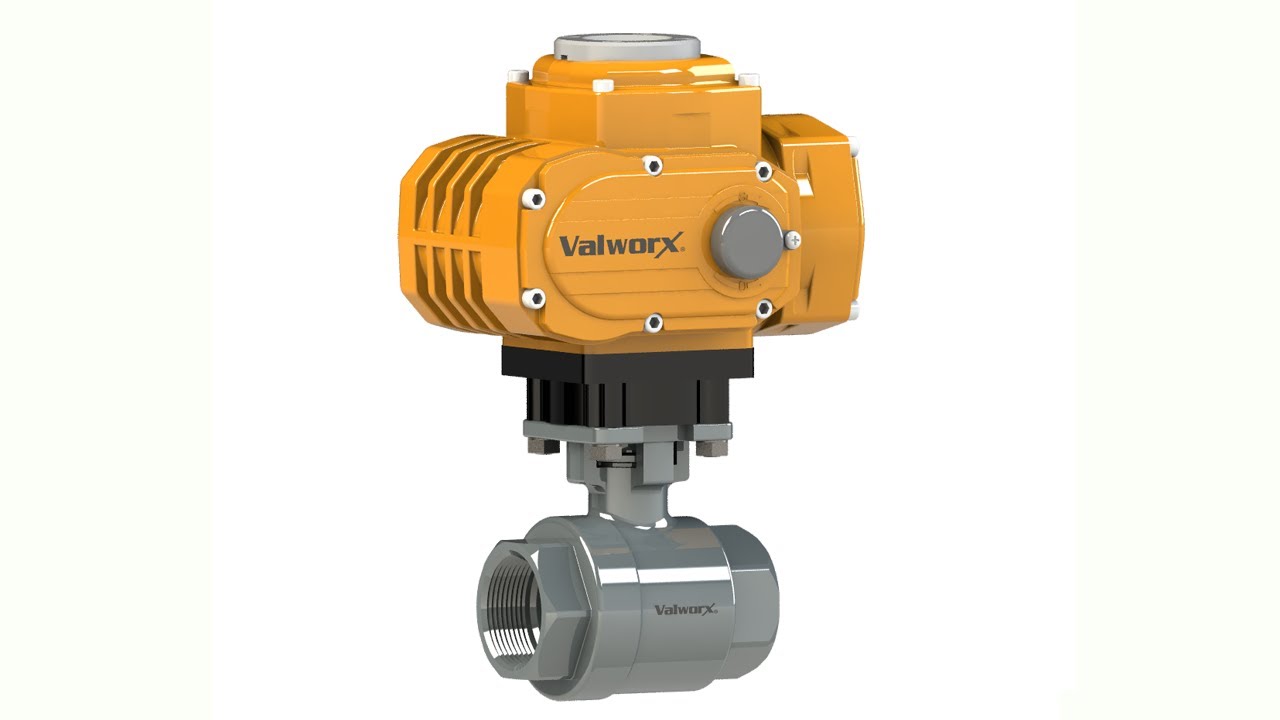