This video introduces the main process of a complete wood pellet production line provided by Shandong Jason Future Environmental Protection Equipment.
A complete biomass pellet production line usually includes the following sections :
Chipping section: This process is to cut wood log, branch,or other materials into small pieces with uniform size about 30*30*5 mm. Jason JS series drum chipper adopts a patented blade roller structure, which increases chipping efficiency and reduces power consumption by 30 -50%.
Crushing section: Usually, a high efficiency hammer mill crusher is used in this section to crush wood chips into particles. where they are crushed by the impact force, shear force, and mutual impact force generated by a high-speed rotating rotor. After screening through a sieve, the materials reach the specified specifications of the product.
Drying section: A rotary dryer is needed if the moisture of wood particle is too high. This process is to reduce the moisture of powder material to a pellet-making favorable level about 15%. Jason series rotary dryer adopts multi-angle lifting plate,which increase the contacting surface of hot air and material, improve thermal efficiency and drying effect.
Pellet making section: Wood particles and powder after dried is pressed and grind-ed into solid wood pellet by wood pellet mill in this section. JS series wood pellet machine is the latest and most efficient model in China. It adopts vertical ring die structure, has the characteristics of high molding rate, steady operation and high output.And enjoys a good reputation in the global market.
Cooling and screening section: The temperature of pellet come out the pellet machine can reach 64-84 ℃. A counter flow cooler is used to cool the produced pellet fuel to room temperature. And vibrating screener will remove the broken pellet.
Packaging section: This process usually adopts automatic packing machine. The cooled finished wood pellet is usually packed in 25kg nylon bags.
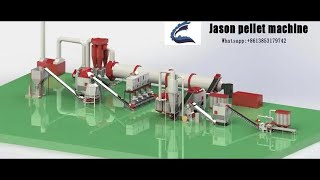