Have questions? We'd love to chat! Send us a message here: [ Ссылка ]
At Viking Pump, we take pride in our vertically integrated manufacturing process. That means we control every step of pump manufacturing. In this Pump Report, Chad walks us through each step of the pump manufacturing process. For more information, visit our website at vikingpump.com
#VerticallyIntegrated #BuildAPump #VikingPump
▬ More Videos ▬▬▬▬▬▬▬▬▬▬▬▬
► YouTube Community: [ Ссылка ]
► All Viking Pump Videos: [ Ссылка ]
► Subscribe to Viking Pump Channel: [ Ссылка ]
▬ Social Media ▬▬▬▬▬▬▬▬▬▬▬▬▬▬▬
► Facebook: [ Ссылка ]
► LinkedIn: [ Ссылка ]
► Website: [ Ссылка ]
The process for manufacturing a pump starts in our foundry, where a mix of raw metals is melted in a furnace. The types of metals and the amount of each is dependent on the specific metal being poured. The temperature and chemistry of the furnace is periodically
checked, and when correct, it's poured into a waiting crucible.
Parallel to the melt process, a sand mold is being formed. Metal from the crucible is
poured in and forms the casting inside. Once it's cooled the sand mold is broken away,
and out comes the metal. If we cut away the gates and risers, the excess parts from it, we get a rough casting. At this point the castings exit the foundry and enter the machine shop. From here the
castings are machined into pump parts. Tolerancing is very important for Viking pumps because it ensures that the pumps meet flow and operate efficiently. Finished parts are then assembled into our various pump models. From there, each pump is given a quality assurance test prior to
shipment. After a quick coat of Viking blue paint, the pump is ready to ship out the door to one of our thousands of customers all over the world. After 110 years that's now been 7,000,000 pumps and counting.
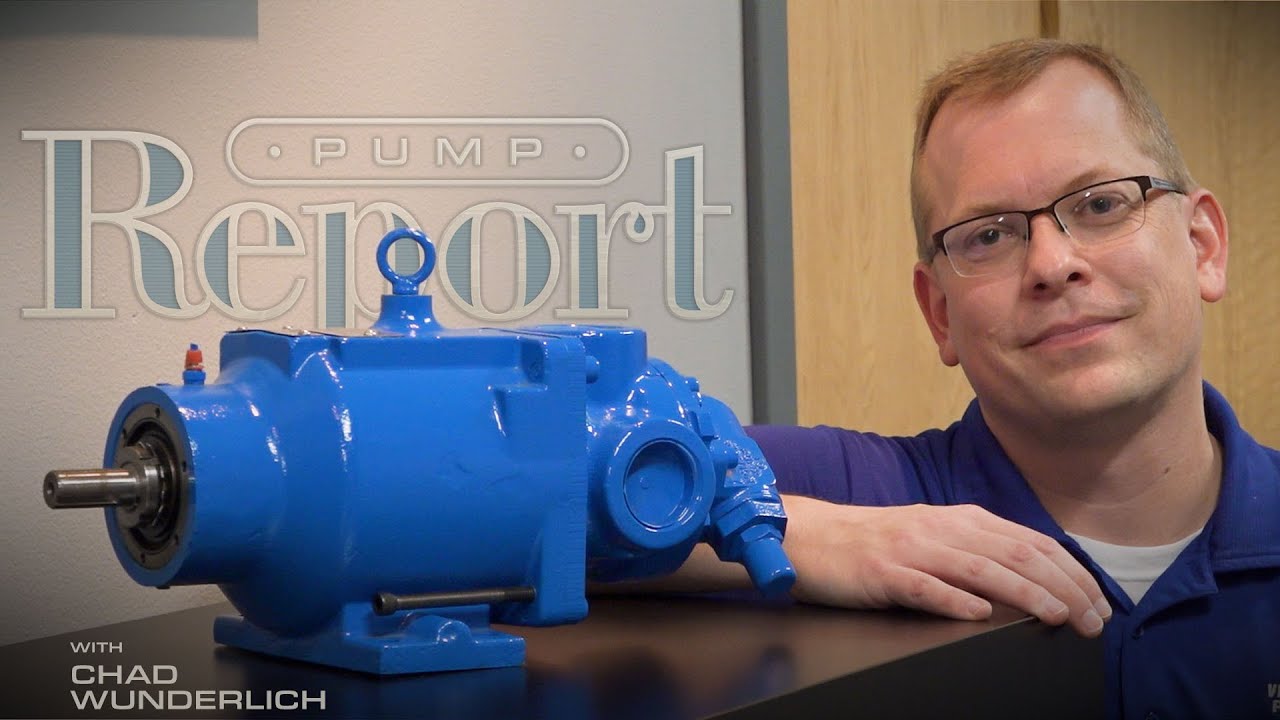