Crystallization process transfer to manufacturing or a contract partner is a critical step. See how chemists and chemical engineers avoid batch inconsistencies, improve filtration and eliminate batch failure. Learn how GlaxoSmithKline (GSK) determined the root cause of the batch inconsistences during crystallization scale-up. [ Ссылка ]
During crystallization process transfer, chemists and engineers use ParticleTrack with FBRM to avoid and troubleshoot batch inconsistencies, improve filtration, and eliminate batch failure. GlaxoSmithKline applied inline FBRM technology to determine the root cause of significant batch inconsistencies during crystallization scale-up. FBRM detected an inconsistency in the seed size and surface area 8 minutes after seed addition. Scientists were then able to correct the source of variability, saving over 14 hours of processing time, improving throughput, and ensuring product consistency upon crystallization scale-up to manufacturing.
Crystallization has demonstrated to provide benefits leading to improved methods for process development, scale-up, and optimization through real-time monitoring.
• Accelerating the characterization of critical operating parameters for increased productivity
• Providing process knowledge that enables real improvements in throughput, yield, and profitability of production scale crystallization
• Enabling the design of more robust processes to assure consistent meeting of crystal specifications and batch-to-batch repeatability
• Identifying undesired events in real time to help ensure product quality
• Eliminating downstream bottlenecks by improving filtration/dryer performance
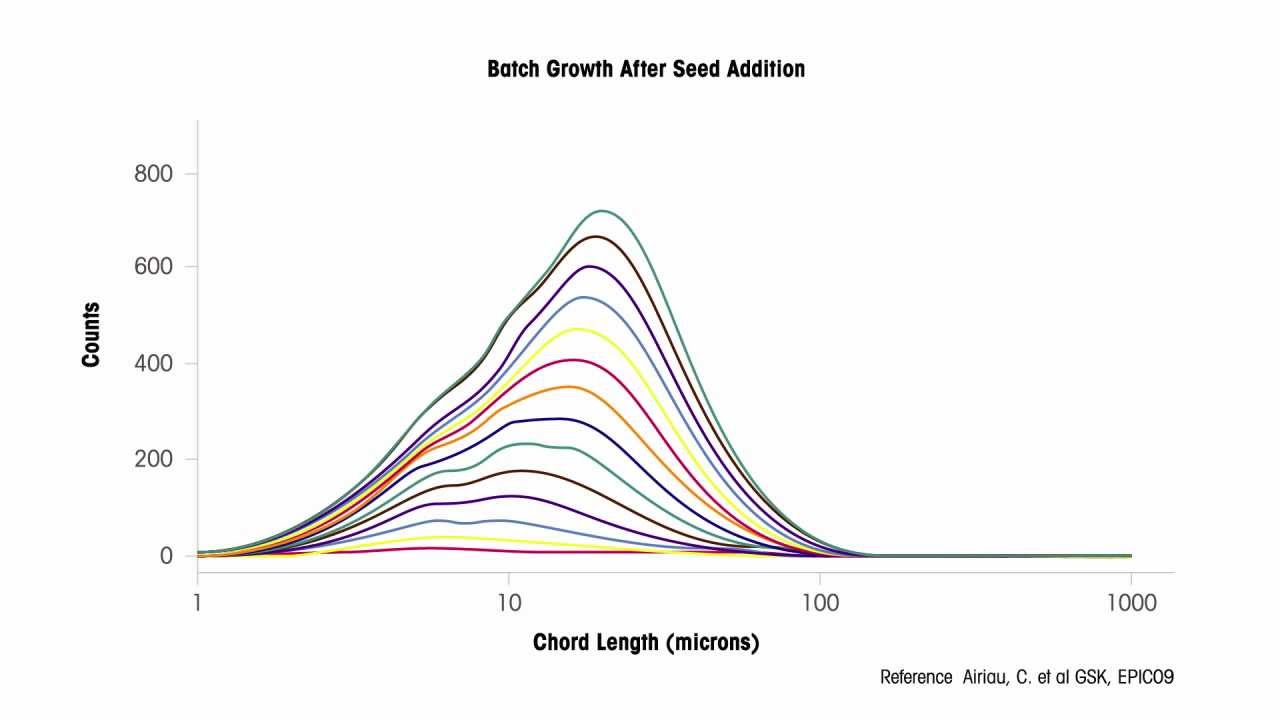