Performing the spindle bearing break-in processes and procedures for a Levin lathe open style headstock, covering the specific tools, the RPM speeds, RPM %’s and time runs and cooling periods, and we finally share the results.
PRECISION MACHINE SPINDLE REBUILDING
Here are the prior released Parts of the Spindle Rebuilding Series you may need to watch before you continue forward here.
In Part 1, our opening video to this series on Precision Machine Spindle, we discuss spindle rebuild preparation and processes. We share the tools, materials and environment needed to rebuild spindles in detail.
[ Ссылка ]
In Part 2, we share how to disassemble a precision machine spindle and a Levin Accessory Spindle is shown however many spindles are discussed.
[ Ссылка ]
In Part 3, we share how to clean the spindle components and wool felt rings, measure for spindle runout and apply the high spot witness mark on a spindle.
[ Ссылка ]
In Part 3a, we share assembling a Levin lathe accessory spindle for the micro-drill, mill, drill press and grinding accessory spindles.
[ Ссылка ]
In Part 3b, we share assembling a Levin lathe open style head stock from start to finish, only the work is not done yet.
[ Ссылка ]
TOPICS COVERED - PART 4
00:00:00 - START
00:00:17 - 0. INTRODUCTION
We share thoughts from the 3 prior video Parts 1, 2 and 3. We share key talking points we covered in this series leading up to this spindle break-in stage of the rebuilding process.
Spindle Rebuilding Tip:
We stress to please STOP if something is wrong with your spindles ability to be genitally hand rotated as it is going to stay wrong. Please do not proceed forward, we share what to do here in this video series ways to make a spindle fix.
00:07:54 - 1. TOOL REQUIREMENTS
We share the tools used in this video, we share what temperature meters do and how they are attached to the spindle or headstock housings in a non evasive manor.
Download our chart that allows you to fill in the blanks with the temperatures, run times and RPM speeds as you perform the break-in procedures.
Your machine table, base and other components should all be completely rebuilt like the spindle now.
00:19:26 - 2. ABOUT THE BREAK-IN PROCEDURE
We discuss the investigation that goes into high tolerance projects like these machine spindles. We share what you are about to perform during the break-in procedures.
The topic of centrifugal forces being gradually applied are shared so to cause the grease to slightly move its way outward from where we placed it with the syringe.
00:29:32 - 3. SPINDLE PREP & MEASUREMENTS
We utilize a 1 micro resolution dial indicator mounted on a small magnetic base for this section, it is mounted to the Levin instrument lathe bed then we take a point of reference reading from our spindles collet seat.
We talk about this setup and share our 10 millionths of an inch collet seat run out, that is 1/5th the allowable amount by the factory.
We share the total break-in setup at the machine bed as well as the magnetic tape holding each of the two “K” Type temp probes.
We share how we monitor and document the temperature reading during the break-in.
00:44:33 - 4. PERFORMING THE BREAK-IN PROCEDURE
We actually bring you along some, over this 3 to 4 hours of the break-in process, come listen to the nice sound our break-in is sharing, you need to be here from start to finish recording your results, following and filling in the downloadable chart to help you keep up the pace and listening to your motor turning the pulley, rotating these brand new precisely greased bearings as they go through the break-in procedures.
00:51:01 - 5. FINAL THOUGHTS
We achieved well within the manufacturer parameters perfect equilibrium results. We also discuss the differences in deep grove bearing and angular contact bearing temperatures and our charted results.
Great day to be at Active Atom we achieved above text book results in this spindle rebuilding and we show that if you follow the processes and procedures and pay close attention to the details of rebuilding a machine spindle, you are more likely to have a higher possibility of achieving the best results possible.
We are off to spindle collet seat grinding, we will share this in Part 5 but remember, grinding is only needed if you need it. Not all spindles need to have there collet seats ground.
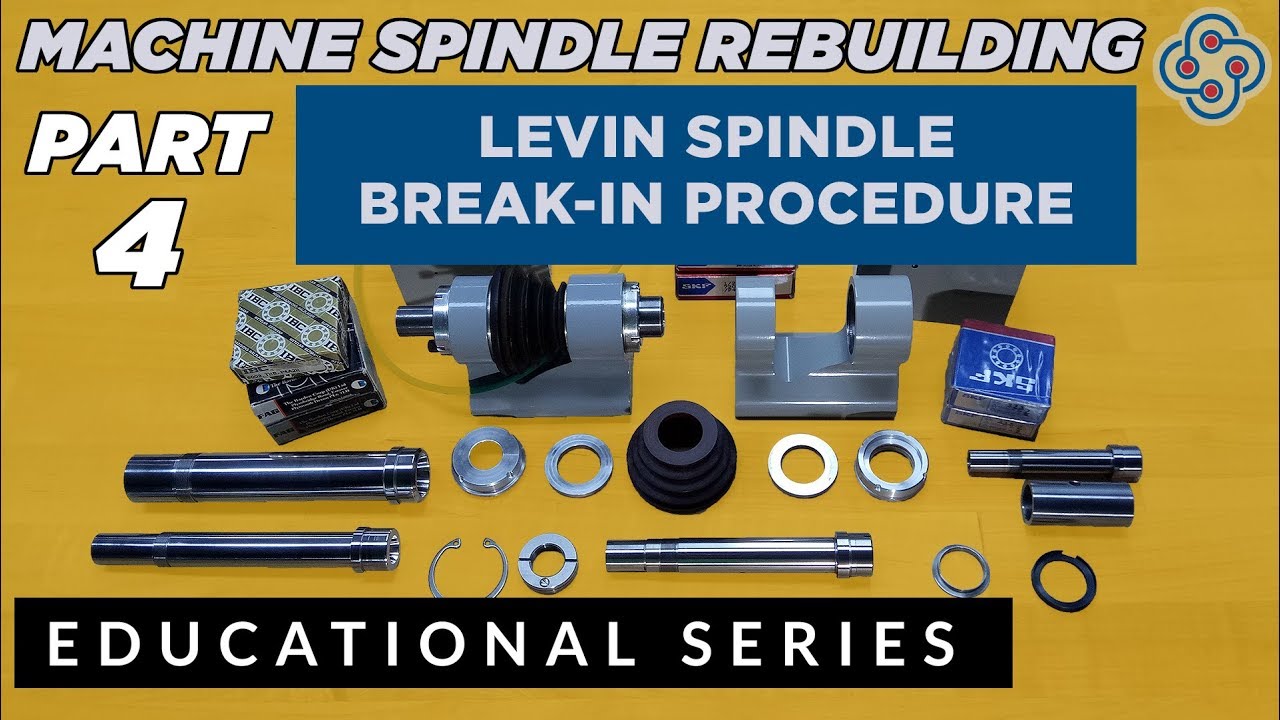