New changes to Heavy Vehicle National Laws (HNVL) for heavy vehicles over 4.5 tonnes gross vehicle mass were be adopted in late 2018. This means a greater onus on occupational health and safety checks and a commitment to safety across the chain of responsibility in the business.
One of the recommendations to those conducting heavy vehicle checks is to develop a Safety Management System (SMS) including controls, safety policy and documentation. It is thus important to investigate available technologies to automate the safety and maintenance process. This can ensure that all regulatory requirements are adhered to and safety inspection reports are safely stored and readily accessible, within the SMS.
A Safety Management System is vital for companies operating heavy vehicles in Australia. The safety of heavy vehicles, employees and the broader community all depend on ongoing, rigorous pre start checks, safety inspections and regular maintenance. For organisations and operations with heavy vehicles, the need for high-end successful monitoring of conditions is a 24-hour, 365-day job. For example: Pre-start inspection is a fundamental part of operating of heavy vehicles and should be carried out before each trip, journey or operation. It is not only the responsibility of both the driver and owner to conduct pre start checks, but also an important record of condition and maintenance. It is therefore important to have the best management tool and checklist available.
[ Ссылка ]
Electronic paperless inspection applications on mobile devices can also include validations that allow or disallow data entry. This is done alongside, providing the user with historical information pertaining to previous inspections, maintenance, pre start checks findings. Paperless/electronic inspection applications should be designed to minimise the amount of data entry and keystrokes required by the inspector/operator by incorporating techniques, ranging from pick lists, check boxes, look-up lists, use of camera or voice recorder, and automatically generated results.
Whatever your operational industry or field, in some way it is highly likely you need a form of pre-start inspection. When you have other business inspections, audit, or quality assurance needs – why spend time and energy having pre-start inspections separate from your other checks? Paperless pre-start inspections are fast becoming the go-to way to undertake any form of pre-engagement check for any organisation or business in any field.
The case for paperless pre-start inspections becomes clearer and more evident when you consider the wealth of technology available to inspectors today. By using a smartphone or tablet, similar to the one we use in our personal lives; inspectors can undertake simple and quick business checks. This could be a safety inspection of an equipment piece; a routine audit or compliance with an industry standard for heating, ventilation and cooling systems; or, a pre-start inspection. Paperless pre-start inspections make use of all the features of the smartphone or tablet device such as the camera, speech-to-text services, and touchscreen. Taking pictures, scanning barcodes/RFID, using voice to record observations, or using the touchscreen to annotate images gives the inspector more tools than a regular paper checklist. For pre-start inspections in rental, it can for example be particularly important to monitor and track the wear and condition of the asset before it is given to a customer. Only by doing this accurately can you comply with rental regulations as well as having no-questions evidence of the condition of the asset. Likewise, for inspections of large machinery with expensive parts to fix or lengthy downtime if issues occur; it may be necessary to make annotations to images to highlight areas of concern for other teams to look at. Small improvements to the inspection process in any pre-start check can mean big things further down the line.
[ Ссылка ]
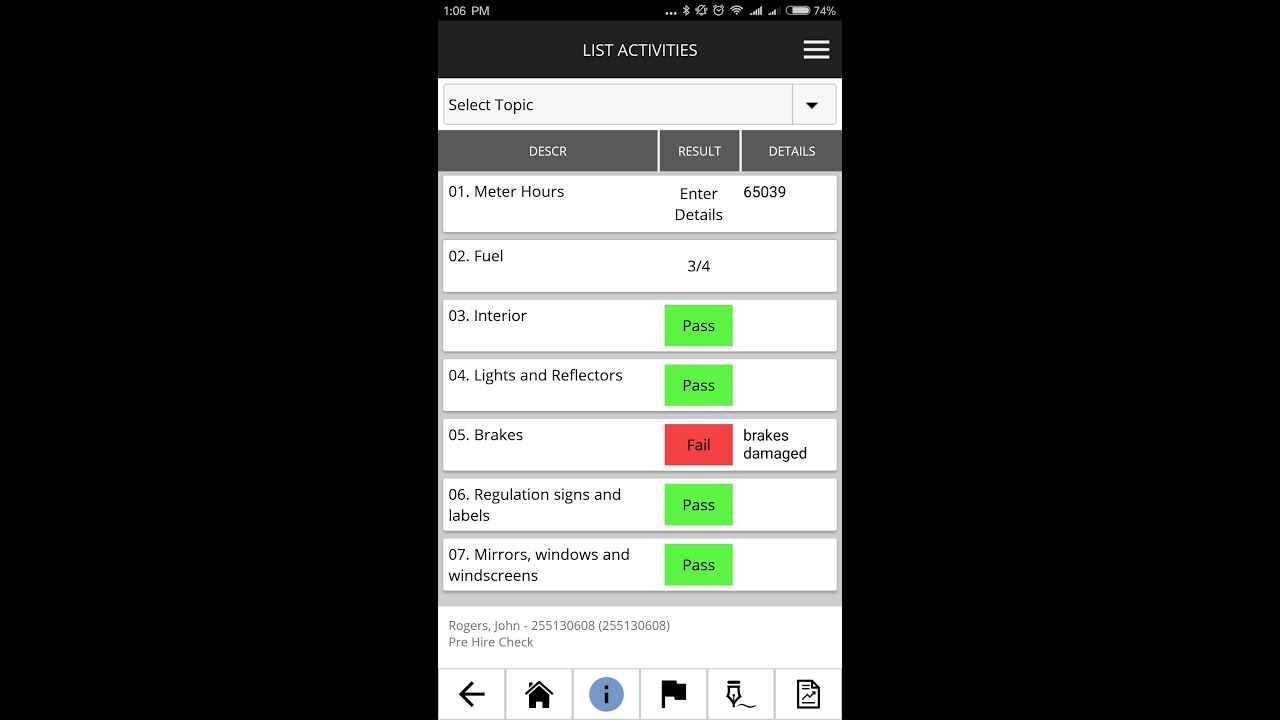