A Fairly Complicated Modern Babbitt Bearing Pour - Rush Job!
This was a challenging job in that I was pouring a very thin babbitt shell into a steel housing to be used in a modern gear box. The job required making a custom pouring mandrel and fixturing rings like I use with many babbitt pours. Due to pouring this into a steel housing, I decided to tin the area that the babbitt would connect to in order to help it properly adhere. Once poured, the babbitt was bored to size rather than just pouring it to a mandrel like I normally do. Unfortunately, the first attempt failed to stick to the steel shell as it should and I had to melt the babbitt out and try again, this time adding locking keys to help secure it in place.
00:00 Introduction
03:25 Turning the Mandrel on the Lathe
09:34 Boring the Fixture Rings
14:56 Examining the Bearing
18:08 Turning Steps on the Fixture Rings
21:59 Tinning the Bearing Shell
26:34 Pouring the Bearings
34:45 Taking the Bearing Apart and Filing the Tops
36:42 Drilling out the Oil Lubrication Holes
37:17 Boring the Babbitt to Size on the Lathe
41:12 Milling OIl Paths
43:36 Delamination....
45:31 Successful Pour and Wrap Up
Support VintageMachinery.org on Patreon:
[ Ссылка ]
Make a one time donation to VintageMachinery via PayPal:
[ Ссылка ]
Please Visit: [ Ссылка ]
Sponsored by:
American Rotary Phase Converters
[ Ссылка ]
Use checkout code "Vintage10" for a 10% discount on all AD, ADX and AI converters!
Hot Shot Heat Treat Ovens
[ Ссылка ]
Use checkout code "VINTAGE10" for a 10% discount!
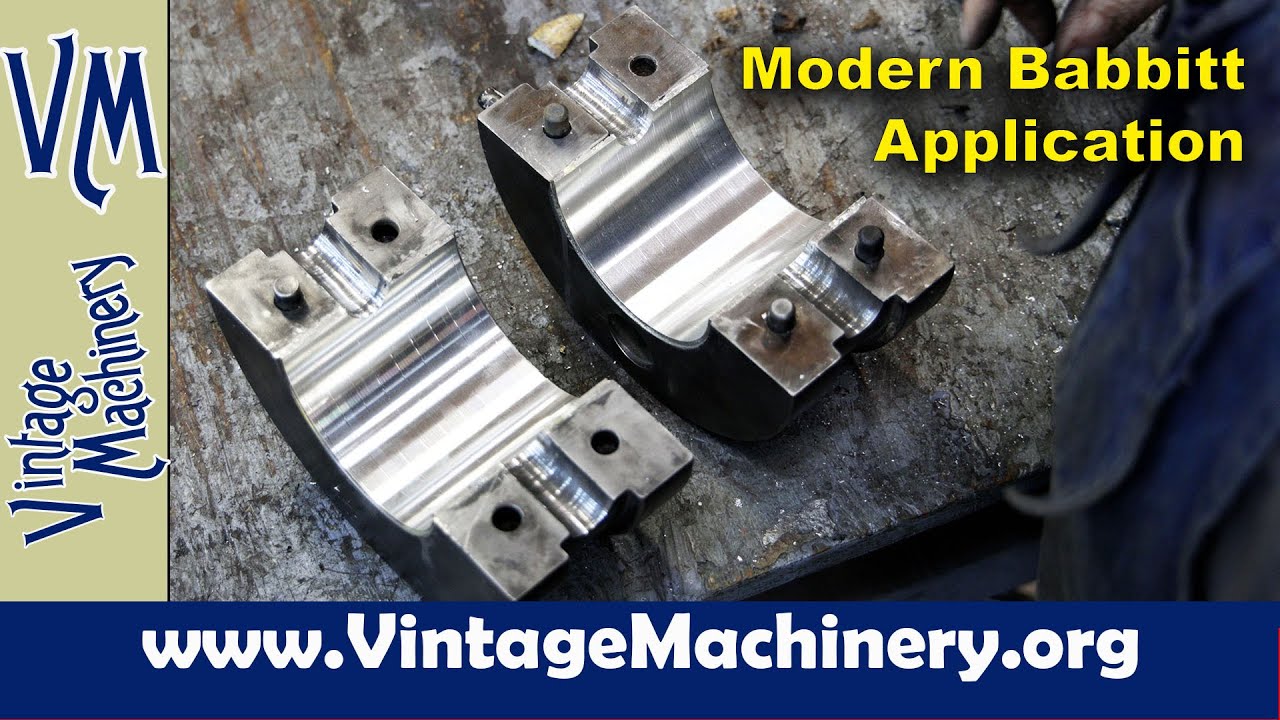