With Digital Depot, there are no more unnecessary stops in train depots. Siemens Mobility's digital train maintenance process makes it possible to monitor trains during their operation, to digitally define and plan all necessary measures and maintenance for the train depot. Hence, optimizing train maintenance through digitalization.
#TrainMaintenance #DigitalDepot #SiemensMobility
Already during the operation, trains are monitored for condition-based and predictive maintenance to define and plan necessary measures. In the depot, maintenance planning and execution are optimized according to lean principles for the shortest throughput times and sustainable resource usage. All spare parts are available through high-speed delivery or 3D printing. This integrated approach reduces up to 20-50% maintenance costs and ensures up to 100% system availability.
Discover more: [ Ссылка ]
▬ Digital Depot – Digital Train Maintenance Process ▬▬▬▬▬▬▬▬▬▬▬▬
Rail traffic is the backbone of the transition to more sustainable mobility. But ensuring sufficient capacity and reliability requires existing rail systems to be utilized as much as possible and at the utmost availability of existing assets. The key is to combine the real and the digital world. The Digital Depot is doing just that it enables maintenance that integrates smoothly with timetables, achieving availability rates of up to 100%.
On the trains in operation, the application suite Railigent collects real-time data and analyzes them using algorithms based on Siemens Mobility's accumulated domain know-how. In this way, users obtain precise information about the health status of the train’s components. This enables the appropriate advance planning of scheduled depot stops.
While the train is in operation, the Digital Depot:
- Optimizes maintenance processes
- Plans ahead all maintenance activities digitally
- Digitally deploys staff
- Orders spare parts or even prints them on site
An automated vehicle inspection provides additional data that are integrated into the maintenance process. The maintenance staff already have all required condition information on hand. This avoids unnecessary work and parts replacements. Mobile user interfaces guide the staff, who are working in parallel in various teams through the digitally planned workflow and the paperless standard-compliant documentation of all performed activities. A final check ensures the proper execution of all maintenance work.
The Digital Depot translates into 30% less depot stops, up to 50% reduction of maintenance and repair costs, the consistent prevention of unplanned downtime, a reduction in the number of required spare trains and up to 100% system availability. That's how Siemens’ Digital Depot helps you make the most of your fleet and pave the way for sustainable future-proof mobility.
#Mobility #MovingBeyond #MovingDigital #SustainableMobility #Sustainability #DigitalWorld #Railigent #OptimizedMaintenance #Siemens
▬ About Siemens Mobility ▬▬▬▬▬▬▬▬▬▬▬▬
Trusted by our partners we are pioneering transportation, moving people sustainably and seamlessly from the first mile to the last. As a leader in transport solutions, we shape connected mobility. With digitalization, we enable mobility operators worldwide to make trains and infrastructure intelligent, to increase value sustainably over the entire lifecycle, to enhance the passenger experience and to guarantee availability.
▬ More Information on Mobility▬▬▬▬▬▬▬▬▬▬▬▬
► Digitalization in Mobility: [ Ссылка ]
► Rolling Stock: [ Ссылка ]
► Rail Services: [ Ссылка ]
► Rail Automation: [ Ссылка ]
► Turnkey rail Solutions: [ Ссылка ]
▬ More Videos ▬▬▬▬▬▬▬▬▬▬▬▬
► All Videos: [ Ссылка ]
► Subscribe to @Siemens Mobility: [ Ссылка ]
▬ Social Media & Website ▬▬▬▬▬▬▬▬▬▬▬▬
► Facebook: [ Ссылка ]
► Twitter: [ Ссылка ]
► Instagram: [ Ссылка ]
► LinkedIn: [ Ссылка ]
► Website: [ Ссылка ]
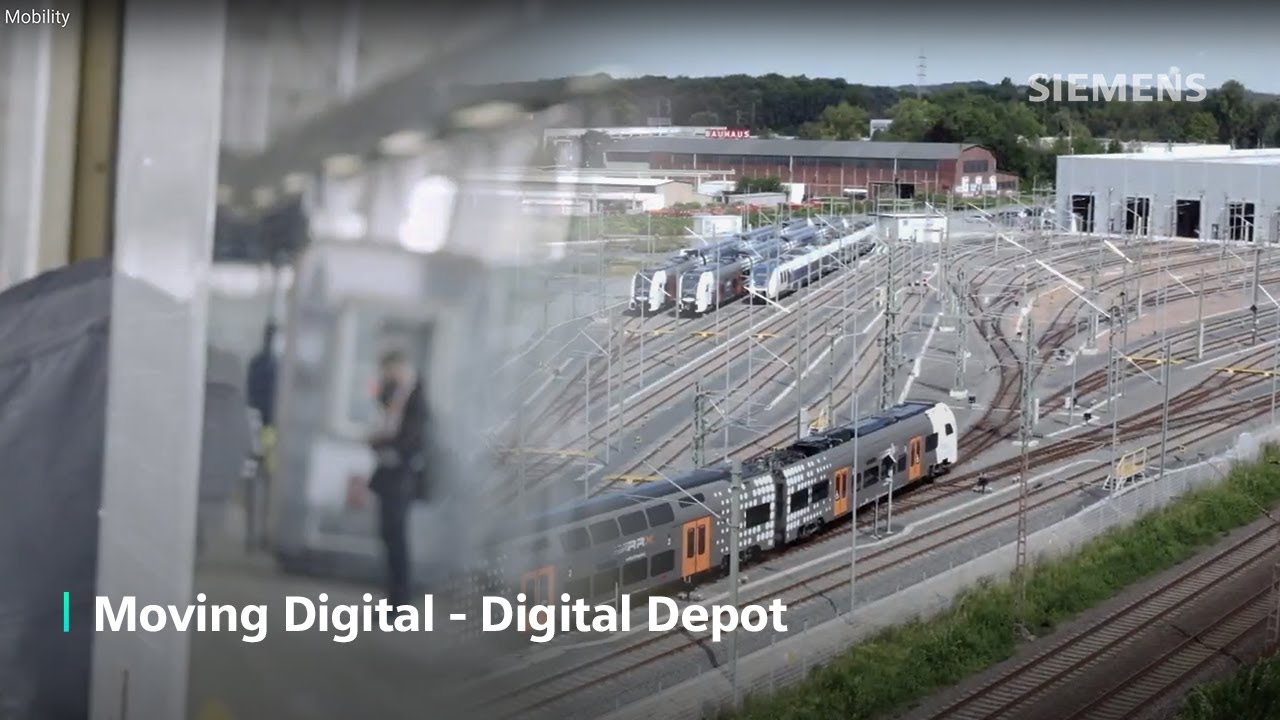