[ Ссылка ]
RECYCLING OF GLASS
This video shows the process steps within a glass sorting plant and explains how to win high quality glass from waste glass.
In contrast to many other packaging materials, glass can be recycled countless times without losing quality. The only requirement for efficient reuse is to extract non-glass residues and to sort the different colours in high quality.
When does the recycling process start?
The recycling process starts with the collection of waste glass either through bottle bank or dry commingled collection / kerbside collection.
What happens inside of such a recycling facility and how does waste glass processing work?
A recycling facility has to be designed due to customers’ needs. This plant was designed to extract non-glass residues from glass with an infeed capacity of 25 tonnes per hour.
First the waste glass material is loaded to feed hoppers to pass into the actual processing hall via a conveyor belt. Here the input material is screened, then cleared of bulky pieces and large contaminants and then crushed. Then the drying process follows. It consists in most of the cases of a rotary drum dryer and a dryer air extraction system that dries the glass and cleans the surface of the glass in one-step. With the drying process designed by REDWAVE, the process can be adapted to different input material compositions by either drying all the input material or selecting a certain grain size to be dried only. By this, the energy consumption at the drying process is minimised with no loss of efficiency.
After that, the dry material is further treated for metallic materials with both ferrous and non-ferrous, being separated from the glass by magnets and eddy current separators.
At the subsequent optical sorting process, the glass which is now called “cullet” is cleared from plastics and other inert materials by REDWAVE sorters with different sensor configurations. Plastics are recognised by the means of near-infrared spectroscopy sensors whilst colour cameras search the cullet for inert materials such as ceramics and stones. Glass with traces of heavy metals such as lead glass and glass ceramics are detected by X-ray fluorescence technology.
Upon detection of unwanted materials, those are ejected by air valves.
Final quality control sorting ensures the highest colour purities of up to +99% in products such as Flint Cullet, Amber Cullet and Green Cullet. With REDWAVE glass colour sorters, even the slightest colour differences can be detected to obtain half-colours such as half-flint from flint for instance.
Before the material is considered finished, the products are independently checked by the REDWAVE automatic sample taker and analyser. The results are then logged for quality assurance.
The sampling paired with REDWAVE mate Smart Plant software will improve the productivity of the recycling process by retrieving and comparing process data provided by REDWAVE mate Smart Machinery. The REDWAVE mate will digitalise your entire recycling plant and will provide comprehensive insights into the recycling process. It is even possible to let REDWAVE mate Smart Plant control certain processes of the plant on its own if the operator chooses.
The obtained cullet is then transferred for its re-use in glass container production.
What was once waste glass has become a high-quality recyclable raw material and it can be recycled again and again.
Glass Recycling reduces the breakdown of primary raw materials and it saves energy through production of secondary raw materials, since melting down used glass uses considerably less energy than melting down primary raw materials.
Brochure describing REDWAVE CX sorting machine: [ Ссылка ]
Visit us at LinkedIn or follow us if you like to be part of our sorting technology family!
[ Ссылка ]
[ Ссылка ]
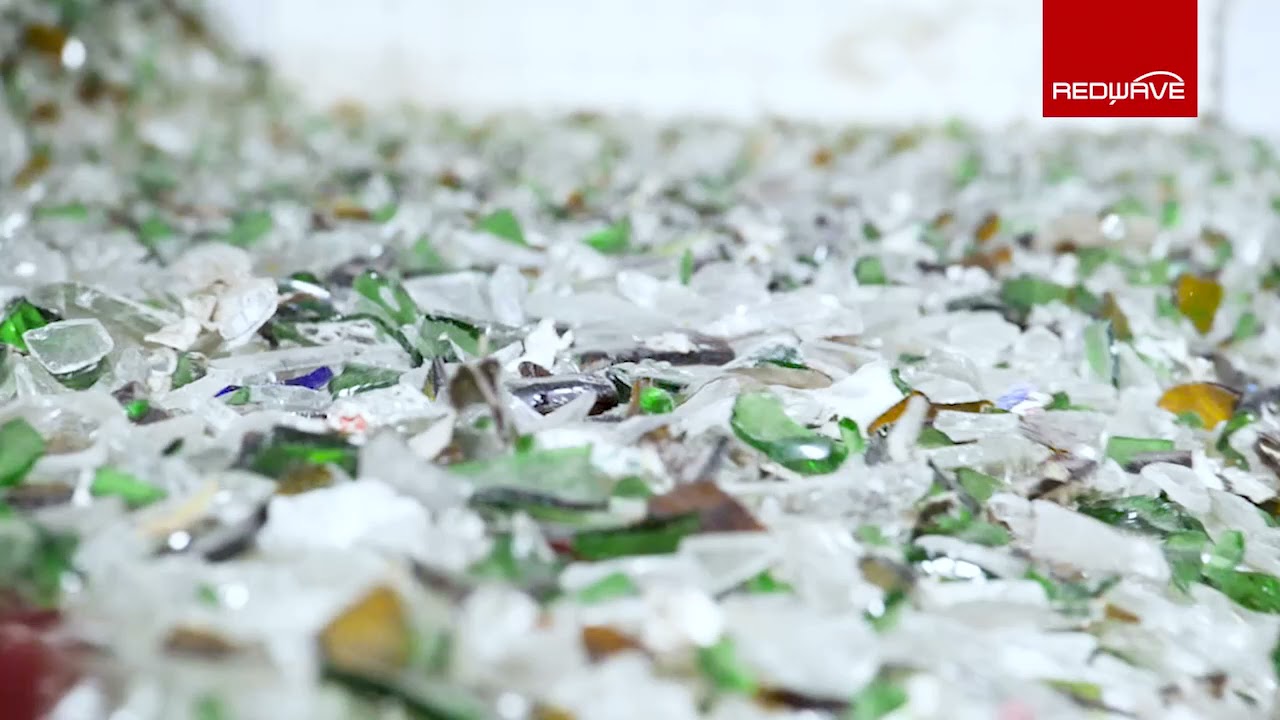