Cold chamber die casting process is operated through molten aluminum alloy material being added into the die shot cell from an independent origin. Since molten aluminum is brought in from an external provider, the cold box casting machine has the capabilities to operate with a lower temperature process.
In the cold chamber die casting process, the molten or liquified metal material must be added for each die shot or production cycle. By requiring molten metal on a regular cycle, this aspect can potentially affect the production rate efficiency for high volume projects.
Also, this cold chamber process requires the use of increased pressure. The high pressure at which the liquid material is pushed into and expands in the die cavity, significantly rank higher than the pressure that is required to operate hot chamber die casting. Pressures of 3,000 psi to 50,000 psi are commonly used during the manufacturing process to fill the mold cavities during the cold chamber process.
Die cast parts that are manufactured through the cold chamber process have advantages that can include: very detailed design, thinner part walls and enhanced mechanical properties.
Cold Chamber Die Cast Process Snapshot
- Aluminum is liquefied through a furnace
- Molten aluminum is then ladled into the die cast chamber
- Plunger forces the aluminum into the cavity under high or low pressure
- The die opens and the plunger moves forward
- Ejector pins force the die cast part out of the ejector die, causing the plunger to retract
- This technique is often used with metals that alloy quickly with iron at high temperatures
- Since these materials would regularly pose problems when melted in a (part-iron) casting machine
- The cold chamber process is most ideal for metal alloys that have higher melting points
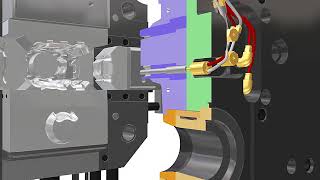