Amorphous alloy core transformer annealing furnace, amorphous ribbon annealing furnace.Email:transformercore99@gmail.com/Whats app:+86 18632727083
1) The role of the annealing furnace:
1. The amorphous alloy transformer core annealing furnace is specially designed for the
annealing and stress-relieving of amorphous transformer cores, and satisfies the stress-
relieving annealing treatment of the formed iron cores under the magnetic field. 2. During the annealing process, nitrogen protection is required to prevent the surface of the
iron core from being oxidized. It can obtain good loss characteristics, so as to achieve the
effect of energy saving and environmental protection of the amorphous transformer. 2)Technical parameters
Specification
Contents
Annealing furnace technical parameters
Quantity 1 Set
Installation Size
Studio size 1600×1600×1800mm (W×D×H) (height is the height from the bottom surface of the
inner chamber to the top surface)
Workpiece rack 4 layers (removable in layers). It can also be entered and exited by a rail-type trolley. pick one of two
Power supply 3N+PE 380V 50Hz
Operating
temperature range
Room temperature~4507
Heating time ≤3 hours
Temperature
uniformity
≤±5°C (refers to the temperature difference between the workpieces during the
annealing process of the workpieces ≤±5°C)
Temperature
fluctuation
≤±1°C;
Heating power 84kw (considering energy saving, heating in four groups)
Blower power 7.5kw
Nitrogen flow
range
0.16-1.6m3/h (adjustable)
Field Current
Connection Bronze
Specifications: 8×80mm, installed at the bottom of the box and well insulated from
the oven body (low voltage). Furnace System Structure
Structure type Monolithic structure. Door opposite door
Door seal The door frame has three seals, and is sealed with ceramic fiber square rope, which
has good sealing performance. Furnace shell
skeleton
Q235 channel steel, made of angle steel welding, after anti-rust treatment, sprayed
with amino self-drying paint. Furnace shell After the Q235 steel plate is treated with anti-rust, it is sprayed with amino self- drying paint. Furnace skeleton Q235 channel steel, angle steel welding, after anti-rust treatment, sprayed with high
temperature resistant silver powder paint. Furnace inner liner Made of SUS304 stainless steel plate, connected by screws and argon arc welding, and treated with high temperature deformation prevention. There are expansion joints
between the liner board and the board, which is convenient for free expansion and
contraction at high temperature. Insulation Materials It adopts high-density high-quality aluminum silicate cotton + ceramic fiber blanket
double combination filling structure. Insulation effect The temperature of the outer surface of the furnace body, from the start of the
annealing furnace to the temperature of the furnace after the furnace temperature
reaches the working temperature, does not exceed 30 °C. Insulation layer
thickness
200mm
Blower System
Air supply method Studio hot air supply mode: vertical air supply from bottom to top (portrait)
Blower The special temperature-resistant centrifugal long-axis motor is equipped with high-
temperature-resistant bearings and high-temperature grease. Blower power 7.5KW
Circulation fan air
volume
8600-12000 m3/h units
Circulation fan air
pressure
765-990pa
Blower impeller Using SUS700*25 multi-wing fan blades, blades and hubs are welded. And do anti- deformation treatment. Heating System
Electric Heaters
1. The electric heating rod is made of U-shaped stainless steel electric heating tube to
reduce deformation. The heating rod is fixed firmly and reliably. The joint is made of
stainless steel nut, and measures are taken to prevent thermal expansion and cold
contraction from loosening.
2. In order to prevent the local temperature of the electric heating tube from being too
high, the heating density of the electric heating tube is controlled at 2-2.5w/cm2. Nitrogen inlet
Access port
location
There are 3 nitrogen filling ports on the back of the box, and the switch is controlled
by a solenoid valve. Automatic switch according to process requirements. And
equipped with a manual flowmeter to control the flow of nitrogen. Nitrogen
external piping
Made of galvanized steel pipe. The joint is sealed with raw tape. Electrode introduction device
Electrode
installation position
Installed on the back of the box and well insulated from the oven body (low voltage). Back out from the side of the oven, the outlet is sealed with a high temperature
resistant gasket. Copper bar extension length: about 200mm. High frequency
magnetron field
power supply
Then connect it with the high-frequency magnetron power supply through the bronze
medal
AC input: 380VAC±20%/BA. DC output: 2000A.
Amorphous alloy core transformer annealing furnace, amorphous ribbon annealing furnace
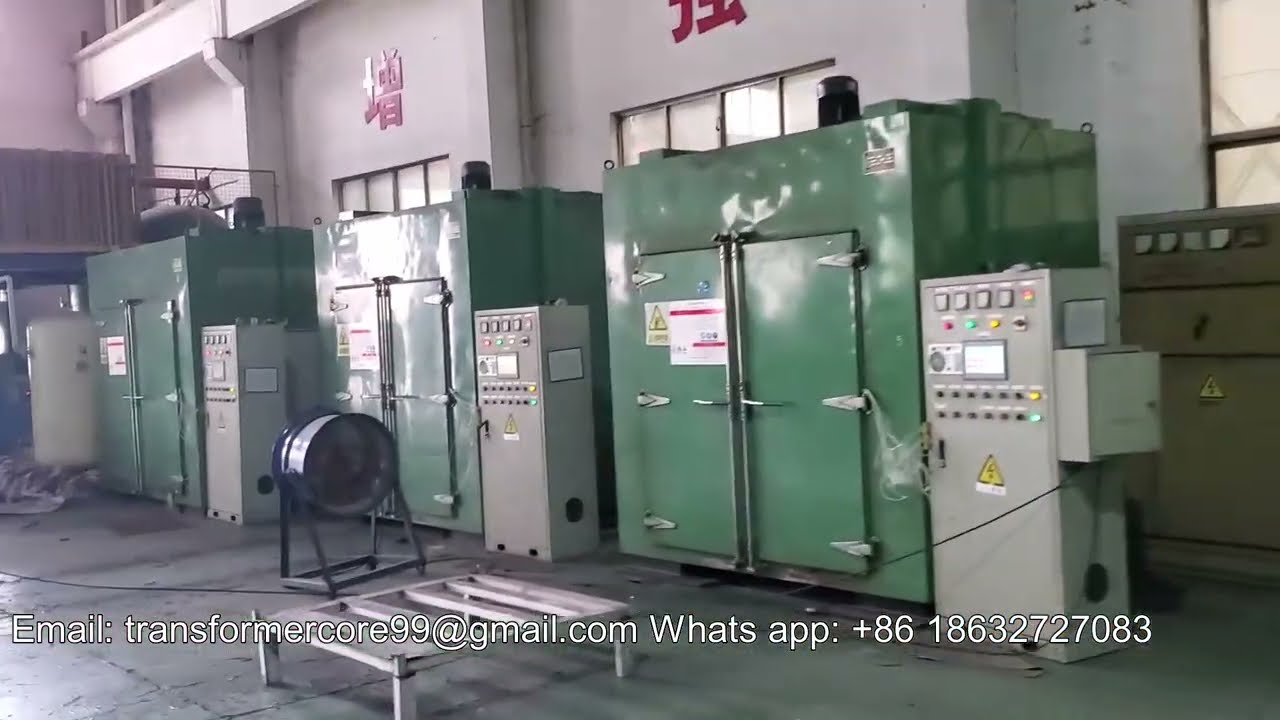